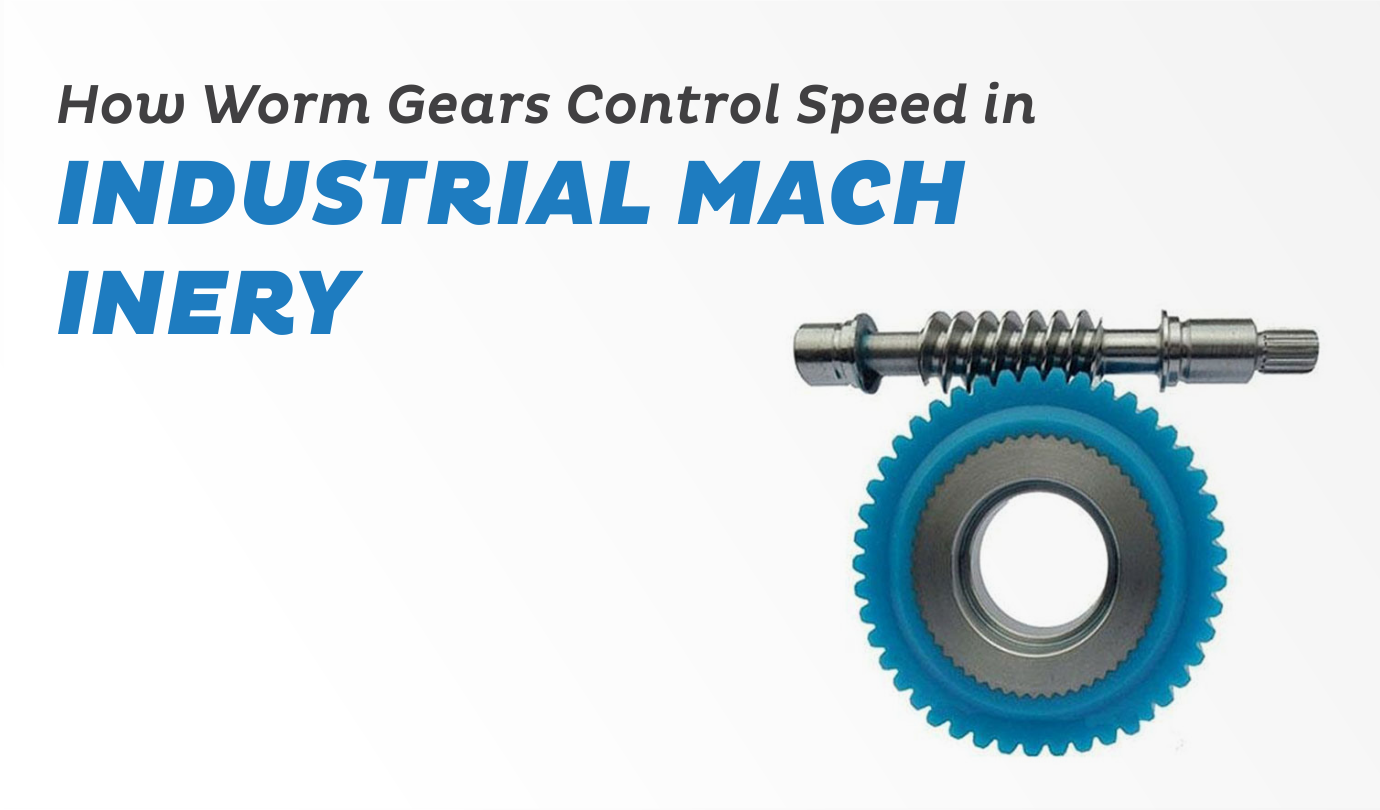
A wheel-shaped gear with teeth is driven by a worm gear, which consists of a spirally threaded shaft called a worm but is basically a screw. The screw and the wheel come together to create a right-angle gearbox when they meet at an angle of 90 degrees. Despite their seemingly simple design, worm gears have proven to be quite effective for managing power and torque in industrial settings. This allows:
- Command over the rate of rotation and the direction of rotation
- Higher torque transmission
Worm gears are not generally the most efficient alternative, but they provide significant benefits for several industrial applications. The tuning peg on an acoustic guitar is the most elementary illustration of this concept. This particular kind of worm gear is the only one that can rotate in either direction. Drives utilized in industrial applications do not have the ability to go in the opposite direction, making them useful for regulating speeds and when braking and/or holding are necessary.
A Worm Gear With A Right Angle Reduces The Speed.
When it comes to decreasing speeds in industrial applications, the gear configuration known as the right angle worm gear is the most prevalent. It can withstand stress loads and overloading without breaking, is adaptable, and is a good value for the money. The number of threads on the worm shaft and the number of teeth on the gear are the two factors that decide the speed reduction ratio. You may enhance the amount of speed reduction by coupling two gear reducers together if that is necessary.
Braking May Be Accomplished With The Use Of Worm Gears
Worm gears would also be used as secondary braking mechanisms due to the fact that they only rotate in a single direction.
Worm gears are often used in the construction of lifts and elevators because of their ability to control load speed and avoid free-fall. When the conveyor system is not utilized, worm gear-based systems will simply lock up rather than move in the other direction.
Two worm gears, one for each direction, are employed in applications that demand movement in both directions. Two worm gears manage these applications. This is a typical configuration for operating automated gates, which increases the level of safety since the gate cannot be broken through or opened by force.
Different Kinds Of Worm Gears
There are three primary configurations for worm drives:
Non-throated
This form only consists of a single moving point that makes contact with the gear as opposed to a continuous thread. Due to the limited amount of contact, this particular form of worm drive is the most susceptible to wear and tear caused by high unit loads.
Single-throated
This variant is able to endure large unit loads with significantly reduced levels of wear. Because of the way its concave helix wraps around the worm, it maintains constant contact with the gear.
Double-throated (also known as hourglass or cone)
Because it includes concave teeth on both the worm and the gear, this design can resist the greatest unit loads without experiencing excessive wear and tear. This is possible due to the fact that the contact surface is doubled.
Worm gears are an excellent choice for low- to moderate-horsepower applications that need substantial speed reduction in addition to small size, high ratios, and high output torque. Worm gears are also an excellent choice for applications in which space is at a premium. Because of this, they might be an excellent choice for applications such as conveyors, tiny machines, and packing equipment. Because of how softly they function compared to other kinds of gear, they are an excellent choice for applications where noise might be an issue, such as in theaters and elevators. Worm gears are also less prone to breaking than other types of gears since they have fewer working components.
Worm drives have the ability to be constructed with either right-hand or left-hand gearing, allowing them to rotate in either clockwise or anti-clockwise direction. Both sections of an internal helical gear need to have the same hand in order to function properly. When using external helical gears that operate in parallel, the hands have to be in the opposite position.
Get High-Quality Worm Gears With Premium Transmission
It’s crucial to use a quality and reputed worm gear manufacturer to make the most of these gears, like Premium Transmission. Contact our team of experts to learn more now!