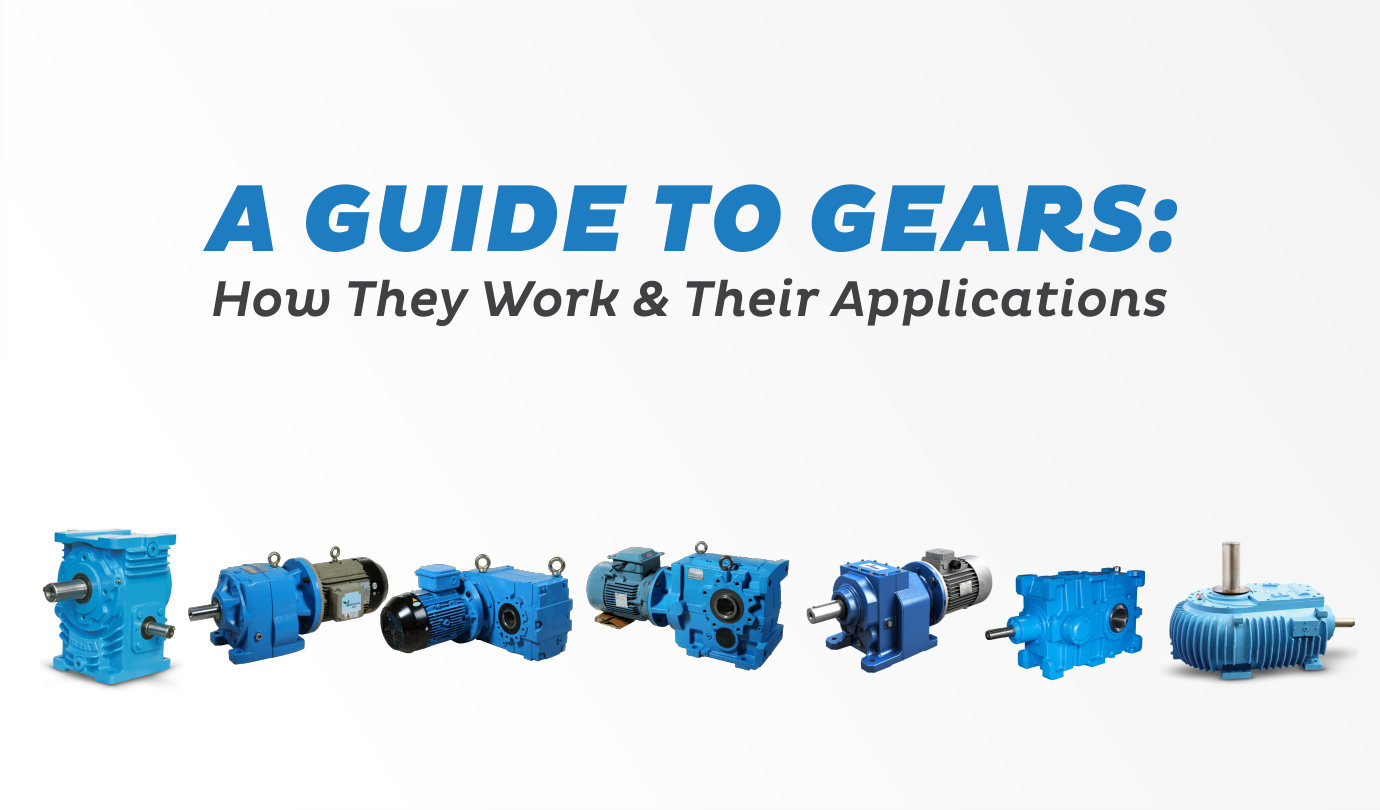
Gears and their mechanical properties are widely used in a number of sectors to transmit motion and power in mechanical devices such as clocks, instrumentation, and equipment, as well as to reduce or increase speed and torque in motorized devices in industries and machines.
Other design elements, including construction of material, gear form, tooth construction, and design of gear pair arrangement, aid in classifying and categorizing the numerous types of gears available. Each type of gear has varied characteristics and advantages, but the requirements and specifications of a specific motion or power transmission application define which type of gear is most suited for use.
This article focuses on gears, investigating the many varieties, and discussing their roles and operations.
An Introduction To Gears
Gears are toothed mechanical transmission elements that are used to convey motion and power between machine components. Gears mesh their teeth with the teeth of another corresponding gear or toothed component when they operate in matched pairs, preventing slippage during the transmission process.
Since each gear or toothed component is attached to a machine shaft or base component, when the driving gear (i.e., the gear that provides the initial rotational input) rotates with its shaft component, the driven gear (i.e., the gear or toothed component that is impacted by the driving gear and exhibits the final output) rotates or translates with it.
The transmission of motion between the driving shaft and the driven shaft might result in a change in the direction of rotation or movement, depending on the design and construction of the gear pair. Furthermore, if the gears are not of similar size, the machine or system has a mechanical advantage, allowing for a change in output speed and torque.
Gear Design Characteristics
Gears come in a wide range of designs, constructions, and configurations to serve a wide range of industries and applications. These varied qualities enable gears to be classed and categorized in a variety of ways, including:
- Gear shape
- Gear tooth design and construction
- Gear axes configuration
Gear Shape
The majority of gears are circular—that is, the gear teeth are placed around a cylindrical gear body with a circular face—but certain non-circular gears are also available. The faces of these gears can be circular, triangular, or square.
The gear ratios (i.e., the ratio of the output to the input) represented by devices and systems that use circular gears are consistent, both for rotary speed and torque. The gear ratio’s consistency indicates that given the same input (either speed or torque), the device or system consistently produces the same output speed and torque.
Devices and systems that use non-circular gears, on the other hand, have changeable speed and torque ratios. Variable speed and torque allow non-circular gears to meet specific or irregular motion requirements such as alternatingly increasing and reducing output speed, multi-speed, and reversing motion. Furthermore, linear gears, such as gear racks, can convert the rotational motion of the driving gear into translational motion (or a combination of translational and rotational motion) of the driving gear.
Gear Tooth Design
Gear teeth are also referred to as cogs, which is why gear is often referred to as a cogwheel, a relatively archaic name. While the preceding part classified gears based on their overall shape, this section addresses characteristics related to their tooth (i.e., cog) design and manufacturing. Gear teeth are available in a variety of design and construction variations, including:
- Teeth structure
- Teeth placement
- Tooth profile
Gear Axes Configuration
The alignment of the axes—along which the gear shafts lie and around which the gears rotate—in connection to each other is referred to as a gear’s axes configuration. Gears use three different axis configurations:
- Parallel
- Intersecting
- Non-parallel, non-intersecting
Gear Selection Considerations
Because gears are used in a wide range of mechanical devices, there are several types and designs available. The suitability of each type of gear and its exact design for a motion or power transmission application is determined by the application’s specifications and requirements. Some of the most important variables to consider while developing and selecting a piece of equipment are:
- Operational and environmental conditions
- Dimensional restrictions
- Transmission requirements
- Design standards
- Costs
Different Types of Gears
There are various distinct types of gear available based on the design characteristics mentioned above. Some of the more popular types of gears used in industry include:
- Spur gears
- Helical gears
- Bevel gears
- Worm gears
- Rack and pinion
Application of Different Types of Gears
Gears are mechanical devices that are utilised in a wide range of mechanical equipment and systems. There are several types of gears available and used in a variety of household, commercial, and industrial applications, including:
- Aircrafts
- Automobiles
- Clocks
- Marine systems
- Material handling equipment
- Measuring instrumentation
- Power plants
- Pumps
Gearboxes, which are devices made up of gears housed within an enclosure or housing, are one of the most common applications for gears. These devices use a variety of gear types, such as worm gears, bevel gears, helical gears, and spur gears, and are designed to perform a specific motion or power transmission operation inside the machine system, such as altering the speed and torque or changing the direction of the output shaft.
Gearboxes, like most gear systems, have a range of applications, such as Conveyors, Agitators, Ball Mills, etc.
Conclusion
There’s no doubt that gears are used across multiple industries and for different applications. However, it’s important to find the right gear for the right application for optimal use. So, if you’re looking for high-quality products, contact our team of experts at Premium Transmission today!